Material Science / Visit StoneCycling
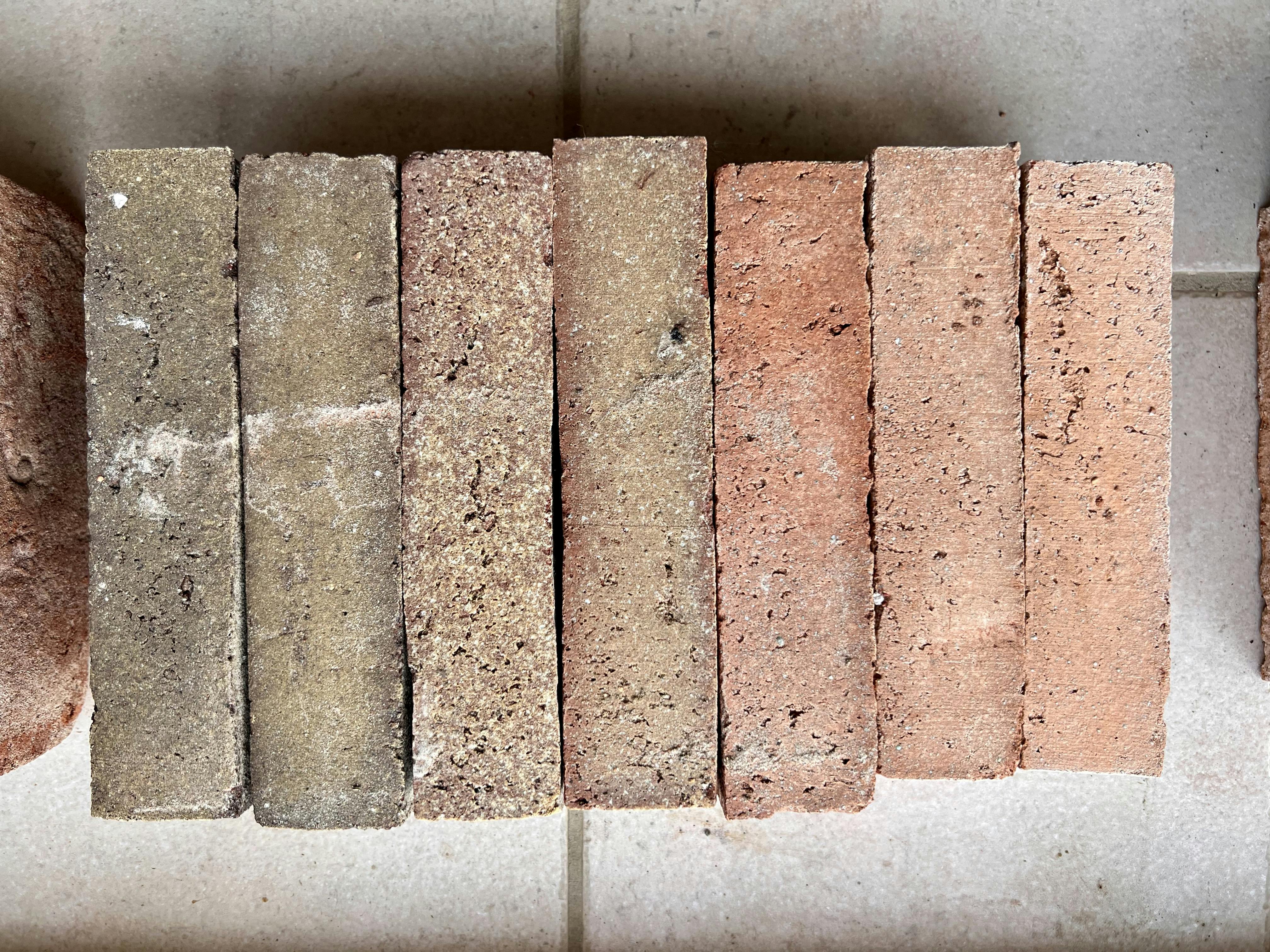
Recently we met with the founders of Stonecycling. As the name suggests, they recycle stones and industrial ceramic waste streams and thus offer sustainable building materials that are made from up to 100% waste.
Buildings have the highest percentage of raw material extraction from nature and are responsible for the largest masses of waste. So the construction industry extracts a lot and wastes a lot of material - and this at a time when the increasing shortage of raw materials in construction is becoming noticeable. Recycling should therefore become the new standard in construction and a serious alternative to conventional building materials. Enough material for recycling is obviously available:
Of course, we couldn't pass up the opportunity to see for ourselves how the innovative bricks are created and paid the Dutch company a visit. Stonecycling collects and sorts construction waste, grinds it according to type and adds 60% waste mixture to the new bricks. This results in products of various colors and shapes. It really took our breath away that Stonecycling makes its bricks entirely by hand. Each brick is cut and packed individually. At the same time, the artisan product is hardly more expensive than conventional bricks.
Furthermore, Sales Manager Esther Kransen particularly emphasizes the value retention of the building materials: "Usually those waste materials will be used in landfill or down cycled in the road construction industry“, she says. At Stonecycling these old toilet bowls, roof tiles, bricks or even recycled glass dust from the recycling process itself go into the new products instead of being processed as granules.
As indicated at the beginning of the text, even bricks made from 100% waste would be possible and are the company's clear goal. But for this to happen, conventional manufacturing processes will have to change. The cooperating factories are currently still designed to use clay as the filling material, so the recipe has been temporarily adjusted to 60% waste while the manufacturing process is being worked on.
The clay that Stonecycling uses is obtained from rivers, where it accumulates renewably as ice melts in the Alps and they clay that forms in the rivers like Neder Rhijn must be removed from the rivers for flood control. Even the temporary compromise in manufacturing thus fulfills the mission of producing sustainably. But how can the manufacturing process change in the long term?
Stonecycling explains to us that they are combining stone manufacturing with a test lab for hydrogen production. In the future, the firing process of the stones will be converted to green hydrogen. At the moment, biogas or certified gas (with reforestation projects) is still used. Since the flames and burning of the gases are different, the hydrogen process is still being tested, which they are doing with their stones. But wouldn't it be wonderful to produce without burning completely?
Yes, dear readers, it is possible. We wouldn’t believe it either. During our visit, CEO Ward Massa gave us an outlook on the future development of the company and welcomed us to what he called ‚the newest Stone Age‘: „The newest material Stonecycling is offering will completely dispense with the burning process. Instead, they will be cured biologically with bacteria.“
Finally, when a product is made of sustainable materials and the manufacturing process is optimized according to sustainable criteria, it goes without saying that distribution is not ignored. The WasteBasedBricks are of course shipped in recycled boxe ;-)
But why is such a well thought-out product not on everyone's lips? Transformation in the construction industry is slow. The industry relies on products that have proven themselves and are also cheaper to obtain. Esther Kransen explains that initially only a small, ambitious customer base is using the products: the 'early adaptors'. But these are important, she says, because they are willing to pay the higher price and initial projects can be realized and made visible.
Through these lighthouse projects that demonstrate quality, larger groups of customers can be made aware. With increasing certification processes and tax incentives for sustainable business, it is becoming more lucrative for companies to be on the lookout for alternatives. We are pleased to see ourselves as early adapters ;-) and to make such a contribution to the transformation of the building industry.
Back